Non-Uniform Thermal Loading — Pooled Condensate
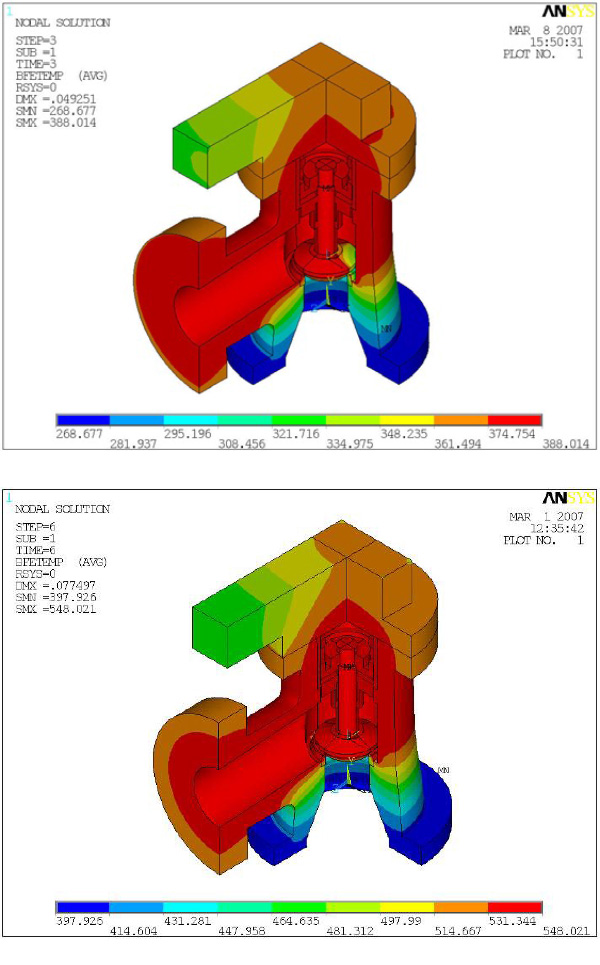
A pilot operated SRV with a vertical discharge suffered from chronic leakage of the main seat. One identified failure mode was that low-pressure leakage, which was common due to low seat load, caused local thermal distortions of the plug and seat ring. The thermal distortions enhanced the leakage and created a deficiency in the contact pressure that was not overcome at increased operating pressures, thereby allowing the leakage to persist even once high seat load was established.
KEI™ performed a coupled steady-state thermal and structural analysis with the cooling effect of seat leak modeled over a 90° span of the seat to determine if low pressure seat leakage could cause sufficient thermal distortions to prevent high pressure sealing. The thermal profile in the valve with and without the seat leak is shown as Figure 1.
The resulting seat contact pressure contours on the seat contact surface for the modeled leak are shown in Figure 2 for an operating pressure of 200 psi and 1040 psi. The seat contact pressure shows (1) the reduced contact pressure persists at high pressure and (2) extreme cooling may cause the loss of sealing in other regions of the seat as suggested by the low contact pressure occurring between -120° and -30° position.