Industries Served
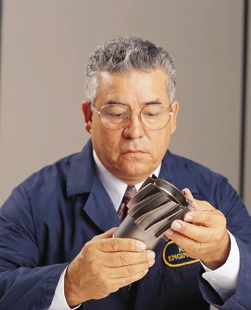
Aerospace and Defense
Kalsi Engineering has a diversified client base that includes equipment manufacturers, oilfield service and petrochemical companies, nuclear power plants, aerospace engineering companies, architect/engineers, industry research organizations, and government agencies. In addition to serving individual clients, we have successfully completed many multiple-client and joint-industry group-sponsored projects.
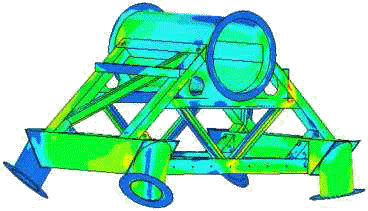
Kalsi Engineering personnel have expertise in stress and thermofluid analysis of mechanical and structural equipment, hardware qualification, and the development of analytical models as well as in the design and testing of hardware for the aerospace and defense industries. We have provided services to NASA, aerospace engineering firms, the Department of Defense, and other government agencies. Our staff has been involved in the Space Station, Space Shuttle, Saturn, and Skylab projects.
Examples
- Design and detailed fabrication drawings for space station mock-up hardware
- Design of a new gaseous cryogenic pressure relief valve with modulating pressure control characteristics to eliminate impact problems for NASA ground support facilities
- Design of a miniature high temperature, high pressure, low noise throttle valve for underwater propulsion systems in defense applications
- Conceptual and detailed design, analysis, prototype development, manufacturing, and testing of unique thermal enclosure systems, heat exchangers, and refrigerator/ incubator modules used in the space shuttle
- Development of analytical models to predict the performance of a spacecraft thermal control system, aero-thermodynamics of reentry vehicles, space shuttle thermal protection system, and ground support equipment
- Test support for wind tunnel, plasma arc chamber, and thermal/vacuum chamber testing