On July 26, 2018 Kalsi Engineering announced a collaborative effort with Packard International, Inc. to provide high pressure washpipe assemblies to the oilfield drilling industry. On May 6, 2019 we announced the completion of a 320-hour test of a pair of 4.5” Kalsi Seals at 9,500 to 9,800 psi and 120 rpm. Now we are pleased to announce that we have completed a 368-hour, 10,000 psi test with a complete three-inch washpipe assembly that is based on our high pressure seal technology and manufactured by Packard International. 165-hours of the 10,000 psi test were performed at 120 rpm, 165-hours were performed at 150 rpm, and 38-hours were performed at 175 rpm. The test was shut down for seal inspection at 368-hours of operation.
The washpipe assembly has two rotary seals, one for pressure retention and the other for partitioning the pressurized fluid from the seal lubricant. The pressure retaining seal was a Super-Wide Plastic Lined Seal™, and the partitioning seal was a spring-loaded KLS® Seal. Both seals were in good condition at the conclusion of the test, as shown below.
Both rotary seals incorporate patented hydrodynamic waves that pump a thin film of lubricant into the dynamic sealing interface during rotation to reduce friction, wear, and seal-generated heat. The high pressure seal is mounted in a floating backup ring that moves laterally to accommodate shaft misalignment and runout, which allows a very small extrusion gap clearance to be used. The partitioning seal is mounted in a laterally floating seal carrier that isolates the seal from runout-related compression changes.
The test fluid was antifreeze pressurized with a piston pump. A moderate amount of cooling was provided to the washpipe by circulating low pressure water through a stationary U-shaped tube located in center region of the washpipe. The coolant circulation rate was about 8 gallons per minute. The antifreeze temperature near the high-pressure seal was approximately 103°F at 120 rpm, 110°F at 150 rpm, and 115°F at 175 rpm.
The next test of the three-inch bore washpipe assembly will be with pressurized drilling fluid. Contact us for more information on the Kalsi Engineering 10,000 psi washpipe assembly.
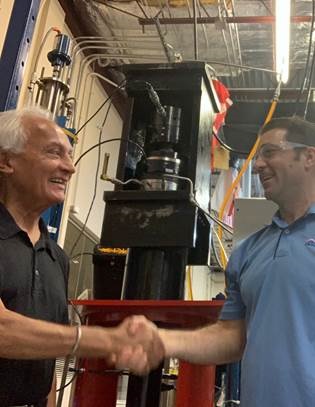
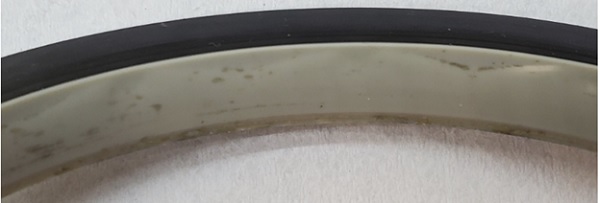
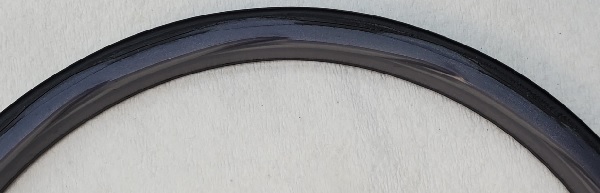