What are the benefits of a wide dynamic seal lip?
Wider oil seal lips increase structural strength and add sacrificial material
A wide dynamic seal lip is one of the features that has enabled Kalsi-brand shaft seals to serve as high-pressure oil seals. The use of a wide seal lip is made possible by hydrodynamic waves that pump a lubricant film between the lip and the shaft during rotation, reducing friction, wear, and seal-generated heat. Conventional elastomeric oil seals typically lack this interfacial lubrication feature and rely on a narrow sealing interface and a light lip loading to minimize heat. The narrow seal lip makes them structurally weak, and unsuitable for high pressure oil retention.
High pressure oil seals are employed to seal the extrusion gap clearance between a housing and a relatively rotatable shaft that is subject to misalignment, dynamic runout, and load-induced lateral deflection. The extrusion gap clearance must be large enough to accommodate the misalignment, runout, and deflection, in order to prevent the shaft from rubbing on the housing. Such rubbing can damage the shaft and housing in ways that lead to seal failure and can also generate enough heat to melt the high-pressure oil seal.
Unfortunately, the larger the extrusion gap clearance, the harder it is for the seal to retain high oil pressure. The pressure forces seal material into the extrusion gap, and lateral shaft motion destroys this extruded seal material by subjecting it to high strain. Over time the seal is destroyed by this extrusion damage mechanism. Failure occurs when the damage works all the way across the width of the dynamic sealing interface.
The relatively wide seal lips of Kalsi-brand high-pressure oil seals provide additional structural strength that helps the lip to resist deformation into the shaft-to-housing extrusion gap clearance, which reduces extrusion damage. The additional structural strength also helps to reduce the contact pressure between the seal and the shaft. In addition to the benefits provided by additional lip strength, wider seal lips also provide additional sacrificial material to resist extrusion damage and third-body seal wear for a longer period.
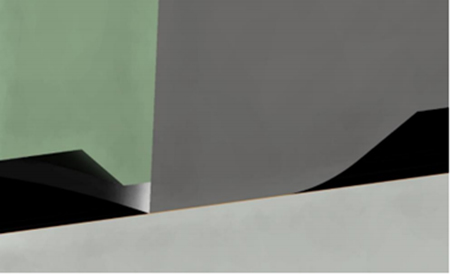
In addition to a relatively wide dynamic lip, with certain Kalsi brand high-pressure oil seals, the dynamic lip is lined with a higher modulus material that supplements extrusion resistance. The pressure capacity of an oil seal can be significantly enhanced through the use of floating hardware arrangements (see here, and here). These arrangements minimize extrusion gap clearance, and minimize relative radial motion between the shaft and the bore that defines the extrusion gap.
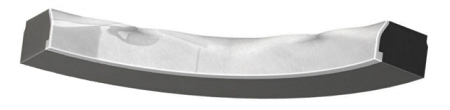
What are the design tradeoffs associated with seal lip width?
Component design always entails tradeoffs, and seal designers and consumers are not exempt. One tradeoff of wider seal lips is increased breakout torque. When breakout torque is a concern, plastic liners and elastomer surface treatments are available to help to reduce startup friction.
Another tradeoff is increased seal generated heat. Kalsi-brand high-pressure oil seals generate heat due to lubricant shearing action and shaft-to-seal asperity contact within the dynamic sealing interface. A wider lip exposes a wider swath of interfacial lubricant film to shear related heat generation, and increased width also results in more potential instances of asperity contact. To a degree, these heat generation mechanisms can be addressed by using more aggressive “Enhanced Lubrication™” hydrodynamic waves. Such waves allow the use of lower viscosity seal lubricants that require less energy to shear. They also reduce asperity contact by approaching closer to a condition of full film hydrodynamic operation. Enhanced Lubrication waves, however, have higher hydrodynamic pumping related lubricant loss. Seal-generated heat also increases with speed, and the widest available lips may be less suitable for higher speeds, depending on the heat transfer characteristics of the application.
Plan to ensure adequate heat transfer from the shaft
The heat generated by a high-pressure oil seal can be significant at higher speeds and is concentrated in the seal lip and the mating portion of the shaft. Elevated seal temperature accelerates various forms of seal degradation, such as loss of strength, compression set, and media absorption. To prevent overheating of the oil seals in high pressure equipment, it is typically necessary to have efficient heat transfer to cool the shaft. In some types of swivels and other equipment, the necessary heat transfer is accomplished by process fluid flowing through the shaft. In other types of higher speed equipment, it may be necessary to provide an independent heat transfer system, such as circulating the seal and bearing lubricant through a heat exchanger.
What widths of seal lips are available?
Standard — The figure of merit we use for comparing lip width is the “standard” lip width of our original product offering. Although these oil seals were considered to have a wide lip at the time it originated, it is now our narrowest oil seal lip. It is primarily offered for applications where breakout torque is a concern.
Wide Footprint — The dynamic lip of a typical Wide Footprint Seal™ is about 1.5 times wider than the standard lip width. This lip width is used for pressure retention and abrasive exclusion in applications where moderate hydrodynamic pumping related leakage is a requirement. Wide Footprint Seals™ incorporate the widest seal lip that suitable for use with our less aggressive zigzag type of hydrodynamic waves. They are also available with enhanced lubrication waves, and with a mixture of zigzag and enhanced lubrication waves, for applications where a higher rate of lubricant leakage is acceptable.
Extra Wide — An Extra Wide seal lip has more than double the width of our standard oil seal lip and is typically used with enhanced lubrication waves. This lip width is recommended for pressure retention in applications that may have larger extrusion gaps and is also useful for abrasive exclusion. With enhanced lubrication waves, moderate lubricant viscosity is often recommended to reduce hydrodynamic pumping related leakage, and to reduce heat generated by lubricant shearing action.
Super Wide — The width of our Super Wide seal™ lip is more than quadruple that of our standard oil seal lip and incorporates enhanced lubrication waves. This seal was developed for abrasive exclusion in applications with slower speeds.
Where to obtain Kalsi-brand high-pressure oil seals
Kalsi-brand high-pressure oil seals are offered for sale under the provisions included in the “Offer of Sale” that is included in the front matter of the Kalsi Seals Handbook™. For available sizes and styles, see our shaft seal catalog. Quotations and additional information can be obtained by contacting our staff by e-mail or online form, or by calling 281-240-6500.
Product is shipped from our Sugar Land, Texas facility, which is in the Houston metropolitan area. We prefer to sell direct worldwide, to maintain close contact with our customers and their equipment requirements, and to avoid “middleman” expenses. Our experienced sales staff is skilled at achieving rapid worldwide delivery.
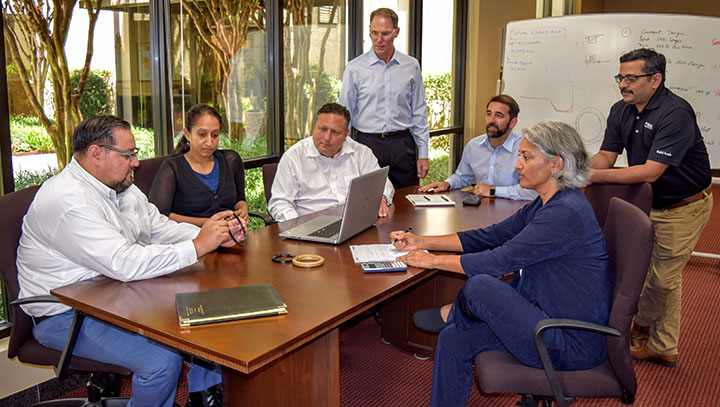