Rotary seals for mud motors
What is a mud motor?
A mud motor is a well drilling tool that uses drilling fluid circulation to rotate a drill bit. The key components are a bearing assembly and a power section. The drill bit is mounted to the lower end of a mandrel that is guided by the bearing section and rotated by the power section.
The power section is typically a progressive cavity positive displacement motor. The motor consists of a stator that is connected to the drill string by threads and a rotor that is connected to the mandrel via a universal joint. Bearings within the bearing assembly locate and guide the rotating mandrel and transfer axial and radial drilling loads between the mandrel and the drill string. The weight of the drill string loads the rotating drill bit against the formation.
Surface pumps force drilling fluid down through the bore of the drill string, and back to the surface through the annulus of the well. The downward flow rotates the rotor of the positive displacement motor, which in turn rotates the mandrel and drill bit. The upward flow sweeps formation cuttings to the surface, where specialized equipment removes the cuttings for disposal.
A small bend angle is often incorporated between the power section and the bearing assembly. With a non-rotating drill string, the bend angle causes the well bore to curve as it is drilled. With a rotating drill string, a straight and slightly larger wellbore is produced. This ability to change from straight to curved hole allows the mud motor to perform directional drilling tasks in oilfield and utility drilling operations.
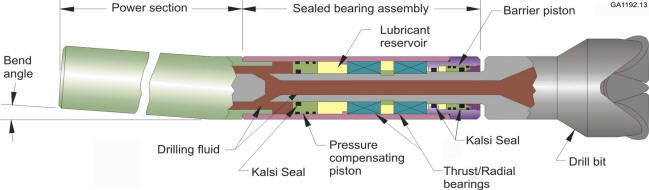
Mud Motor Sealed Bearing Assemblies
A mud motor sealed bearing assembly, shown schematically above, typically uses journal bearings to guide the mandrel radially and rolling element bearings to transfer thrust loads. The use of journal bearings allows the diameter of the mandrel to be maximized, for increased strength and durability in operating conditions that may include extreme torque and side loads. The use of oil lubricated bearings provides accurate mandrel guidance and allows for compact axial length. These features facilitate short radius oilfield drilling. The relatively low cost of oil lubricated bearings also helps to reduce repair and maintenance costs, compared to mud lubricated bearings.
In a sealed bearing assembly, rotary seals are used to retain the bearing lubricant and exclude the drilling fluid and abrasive cuttings. The pressure of the bearing lubricant is typically balanced to the ambient well pressure by an axially movable pressure compensating piston.
The mud flow is communicated from the wellbore to the well annulus via relatively small hardened ports. The flow through these ports causes a pressure drop, making the annulus pressure considerably lower than the wellbore pressure. A rotary seal in a fixed axial location is provided to retain this pressure difference. The magnitude of the pressure difference depends on various factors, including the locations of the hardened ports relative to the pressure compensating piston and rotary seals. Normally, some of the hardened ports are in the drill bit. Others may be positioned to reduce pressure across the pressure-retaining seal.
In the schematic above, the pressure compensating piston balances the pressure of the bearing lubricant to the pressure of the wellbore, and a fixed location seal retains the difference in pressure between the bearing lubricant and a barrier lubricant. The pressure of the barrier lubricant is balanced to the pressure of the wellbore by an axially movable barrier piston. The barrier piston helps to limit lateral shaft deflection, which facilitates the use of a beneficially small “extrusion gap” clearance between the housing and mandrel at the pressure-retaining seal. The schematic is provided just to provide a representative example; various other arrangements are possible. A few examples are included below.
In the schematic above, the rotary seals that are mounted in the pressure compensating piston and the barrier piston are exposed to little or no differential pressure. The pressure retaining seal and the low pressure mud seals each face unique challenges. Kalsi Engineering has developed specialized seals directed at these challenges that represent state-of-the-art in mud motor seal technology. The dependability, ease of maintenance, and favorable economics of Kalsi-brand mud motor seals are confirmed by their widespread use.
Hardware design is critical when implementing rotary seals in challenging oilfield applications. Various factors can influence seal performance, including extrusion gap clearance and length, bearing implementation, mandrel flexibility, shaft surface treatment, etc. As such, a systems approach is required when designing a mud motor sealed bearing assembly. Comprehensive guidelines for implementing Kalsi-brand rotary seals in various types of rotating equipment are included in the Kalsi Seal Handbook. Chapter E3 is provided as an index to the information within the handbook that relates to drilling motor seal implementation. We also offer an oilfield seal-related training class.
Contact Kalsi Engineering for More Information
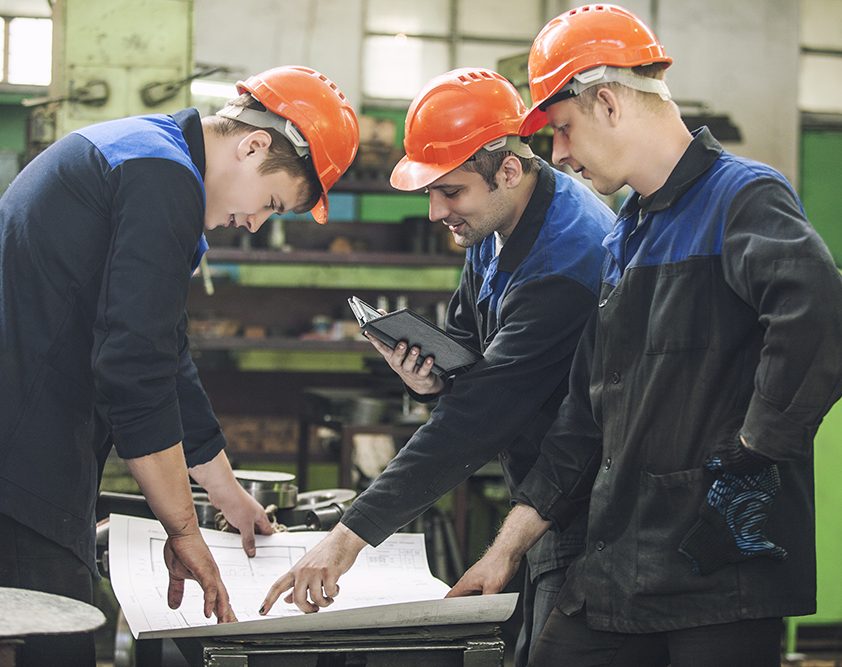
Kalsi Engineering, Inc. is a leader in providing products and services to the energy, petrochemical, manufacturing, and mining industries. Kalsi Seals are world-renowned for their state-of-the-art status, the result of our pioneering research in hydrodynamic lubrication. In addition to these products, Kalsi Engineering also provides engineering consulting services backed by decades of experience in the engineering field.Whether your company is interested in purchasing oilfield seals or needs an experienced engineering resource for your next project, Kalsi Engineering can help you find the best solutions. Contact Kalsi Engineering today to request a quote, or to learn more about how to use Kalsi brand rotary shaft seals for your application. See our shaft seal catalog for available sizes of mud seals.