Introduction to the Submerged Dredge Pump Seal Application
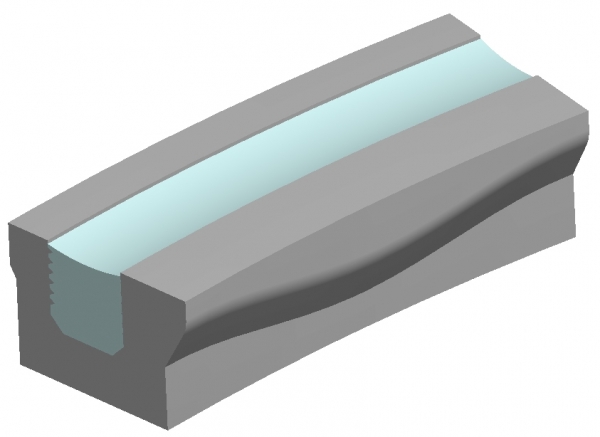
Submerged dredge pumps are used to excavate sediment from harbors, channels, and other waterways to maintain appropriate water depth. Such pumps are a critical sealing application because of the high cost and downtime associated with replacing the large diameter impeller shaft bearings when they become flooded with abrasive-laden saltwater. Since the pumps are filled with lubricant, environmental concerns also exist when seal failure causes the pump lubricant to be dumped into the waterway. Pump operating conditions include significant shaft surface speed (800 ft/minute typical), dirty water conditions (sand & gravel), shaft impact loads from encounters with various sizes of submerged objects, and environmental pressure due to the submerged depth of the pump.
Introduction to Kalsi Seals
Kalsi Seals were originally developed for the harsh oilfield downhole drilling environment. They have now been used successfully in submerged dredge pumps and gearboxes for several years, and have proven to be superior to conventional face seals. The conventional seals have a long history of being prone to problems such as galling, seizure, premature failure, and catastrophic failure. It isn’t unheard of for such face seals to leak significantly while still on the deck, before being used.
Although other types of Kalsi Seals may be even more appropriate as dredge pump seals, the Silicone-Filled Kalsi Seal (shown above) is the Kalsi Seal that is in most widespread use in submerged dredge pumps. The Filled Kalsi Seal incorporates a soft silicone energizer that reduces contact pressure at the dynamic sealing interface. The lubricant-side of the dynamic lip (see below) incorporates a wavy edge that hydrodynamically lubricates the dynamic interface. This combination of features minimizes running torque and seal-generated heat.
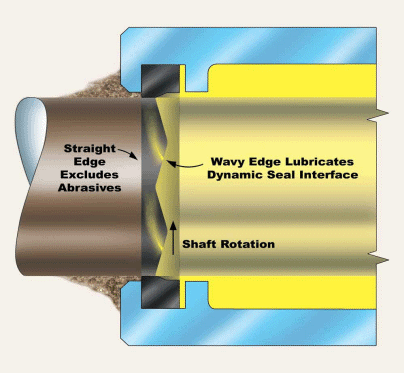
How Kalsi Seals Work…
Kalsi Seals are installed in a housing groove and compressed against a shaft, and seal statically in the same manner as other interference-type seals, such as O-rings.
The dynamic sealing lip incorporates a wavy hydrodynamic edge on the lubricant side, and an abrupt circular exclusionary edge on the environment side. When shaft rotation occurs, a thin lubricant film is hydrodynamically wedged into the dynamic sealing interface by the waves. This hydroplaning effect lubricates the seal and shaft, preventing the typical dry rubbing wear, high running friction and heat associated with conventional seals, allowing higher pressure and speed combinations and providing long life.
When rotation stops, the hydrodynamic lubricating action stops, and static sealing is reestablished. Click here for slow motion seal animation of seal lubrication.
Application Support
General seal implementation guidelines are provided in the Kalsi Seals Handbook™, which is available online here. Experienced personnel are also available to provide technical support. If you would like Kalsi Engineering to review your dredge pump seal application, please download an application questionnaire in PDF or Word format, and return it to us by e-mail or fax (281-240-0255). Alternately, you can forward your seal questions by e-mail, or call us directly at 281-240-6500. For information on available sizes, see our shaft seal catalog.
Kalsi-brand rotary shaft seals are offered for sale under the terms and conditions of the “Offer of Sale” that is included in the current revision of the Kalsi Seals Handbook.