Many rotary seals that partition drilling fluid from lubricant are used with lubricant overpressure, which improves the ability of the seal to exclude abrasives. With partitioning seals, the typically recommended radial extrusion gap clearance between the shaft and the seal carrier is 0.020”. This relatively large clearance helps to reduce abrasion of the seal and the shaft.
Various systems are used to produce lubricant overpressure. Because of the relatively large extrusion gap clearance, the targeted lubricant overpressure is relatively low. Various circumstances exist where the actual lubricant overpressure may temporarily be much greater than the intended overpressure. For example, the pressure of the drilling fluid can drop rapidly when the mud pumps cut off, and the lubricant overpressure system may respond more slowly. The resulting temporarily high lubricant overpressure, combined with the relatively large extrusion gap clearance, can cause pressure-related extrusion damage to the partitioning seal.
The Super Wide Seal™ was developed to provide improved resistance to temporarily high pressure, and to have more sacrificial material to resist abrasive wear. The tests referenced below were performed with 2.75” diameter Type F Super Wide Seals. The 80 and 200 rpm rotary speeds were selected to cover the typical speed range of an oilfield power swivel. All of the tests were conducted with an ISO 68 viscosity grade lubricant and a nominal radial extrusion gap clearance of 0.020”.
In a 2018 blog, we reported on 80 and 200 rpm tests with a drilling fluid environment and lubricant overpressure that ranged from 15 to 200 psi. The good condition of the Super Wide Seals at the conclusion of these 212 and 305-hour tests makes them candidates for partitioning service in power swivels and similar applications.
In a 2019 blog, we reported on a 200 rpm test of a Super Wide Seal with a continuous lubricant overpressure of 1,500 psi. The seal was in good condition after 95-hours of 1,500 psi operation.
We have now performed 80 rpm tests with 1,500 psi continuous lubricant overpressure. The 80 rpm tests were performed to evaluate the ability of Super Wide Seals to operate hydrodynamically with an ISO 68 viscosity lubricant at the lower end of the typical operating speed of a power swivel. One test was stopped at 113.6 hours, and the other was stopped at 138.8 hours. The seals were still in good condition, as shown below. Based on these excellent test results, Super Wide Seals should tolerate temporary exposure to 1,500 psi lubricant overpressure when used with 0.020” radial extrusion gap clearance.
During this testing program, we learned that the breakout torque of Super Wide Seals is high, owing the large amount of material engaging the shaft. For this reason, the 80 rpm tests at 1,500 psi were conducted with PN 739-1-11 LF Seals. These seals have a low friction surface treatment to reduce breakout torque.
Contact the Kalsi Engineering Seal staff to learn more about our rotary seal testing and the testing of the Super Wide Kalsi Seal.
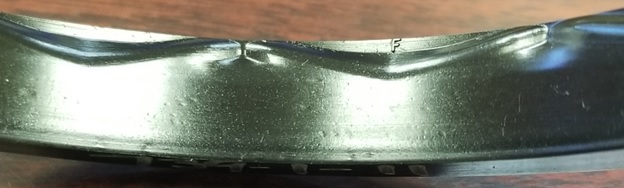
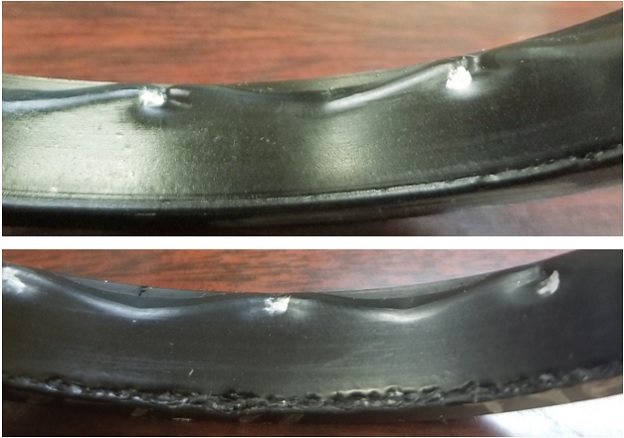