Review of a mud motor design trend
Mud motor sealed bearing assemblies (Figure 1) typically have a “pressure retaining seal” location where a rotary seal is exposed to the pressure difference between the bearing lubricant within the tool and the drilling fluid in the annulus of the well. Such seals bridge the extrusion gap clearance between the end cap and the mandrel of the mud motor.
As revealed by the published literature, over time there has been a design trend to eliminate the deflection limiting outboard barrier piston. This exposes the pressure retaining seal to wellbore abrasives, and additional mandrel deflection. The increased deflection requires larger extrusion gap clearance, in order to avoid damaging metal-to-metal contact between the mandrel and the end cap. The larger extrusion gap makes the pressure retaining mud motor seal more prone to extrusion damage. The exposure to drilling fluid abrasives also exposes the seal to third body abrasion.
Introducing advances in mud motor seal design
When adequately lubricated, wider dynamic lips have improved resistance to extrusion damage. Wider dynamic lips also provide more sacrificial material to accommodate extrusion damage and third body wear. Knowing this, we set out to develop hydrodynamically lubricated seals with increased dynamic lip width, compared to existing 507-series mud motor seals. Two important milestones have been achieved. First, we developed a seal with a moderate increase in lip width that fits in the 0.289” wide groove that is used by existing 507-series mud motor seals. Second, we developed a mud motor seal with a significantly wider dynamic lip width that requires a wider than typical seal groove.
Testing moderately wider mud motor seals
We initiated an R&D project to see if we could develop a seal that is interchangeable with a 507-series mud motor seal but has a wider dynamic lip. Tests were conducted with 2.75” (69.85mm) diameter seals with a dynamic lip that is moderately wider than that of 507-series seals. The rotary speed was 480 rpm (345.6 sfpm) and the ISO 320 viscosity grade lubricant was maintained at 162°F (72.2°C). Testing was conducted at 15, 500, 1,000, and 1,500 psi using a 0.010” radial extrusion gap clearance. Leakage per seal ranged from 0.19 to 0.42 ml/per hour, which is within the normal range of 507-series seals. Contact us for additional information.
Testing extra wide mud motor seals
We also initiated an R&D project to determine if we could develop an “Extra Wide” Hybrid Seal™ that could be used as a mud motor seal. Extra Wide Seals have a dynamic lip that is significantly wider than that of the 507-series seals that were developed for service as mud motor pressure retaining seals.
Our testing program took into consideration the fact that hydrodynamic interfacial lubrication decreases as lubricant viscosity decreases at higher temperatures. It also took into consideration the fact that hydrodynamic pumping related leakage increases as viscosity increases at lower temperatures. Our seal design goal was to provide adequate interfacial lubrication with an ISO 320 viscosity grade lubricant at 302°F (150°C) without having an excessive hydrodynamic pumping related leak rate with an ISO 460 viscosity grade lubricant at 162°F (72.2°C). Testing was performed with 2. 75″ (69.85mm) diameter seals operating at 480 rpm (345.6 sfpm).
Testing was conducted at 15, 500, 1,000, and 1,500 psi using a 0.020” radial extrusion gap clearance. By comparison, 507-series seals were developed using a 0.010” radial extrusion gap clearance. The seals were in good condition with modest extrusion damage at the conclusion of the tests, and leakage was within the normal range exhibited by 507-series seals. Contact our engineering staff for additional information.
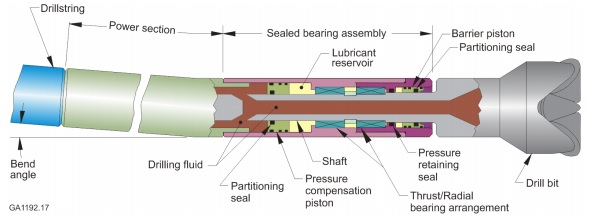